8 Best CAD Software for Aerospace Engineering in 2025
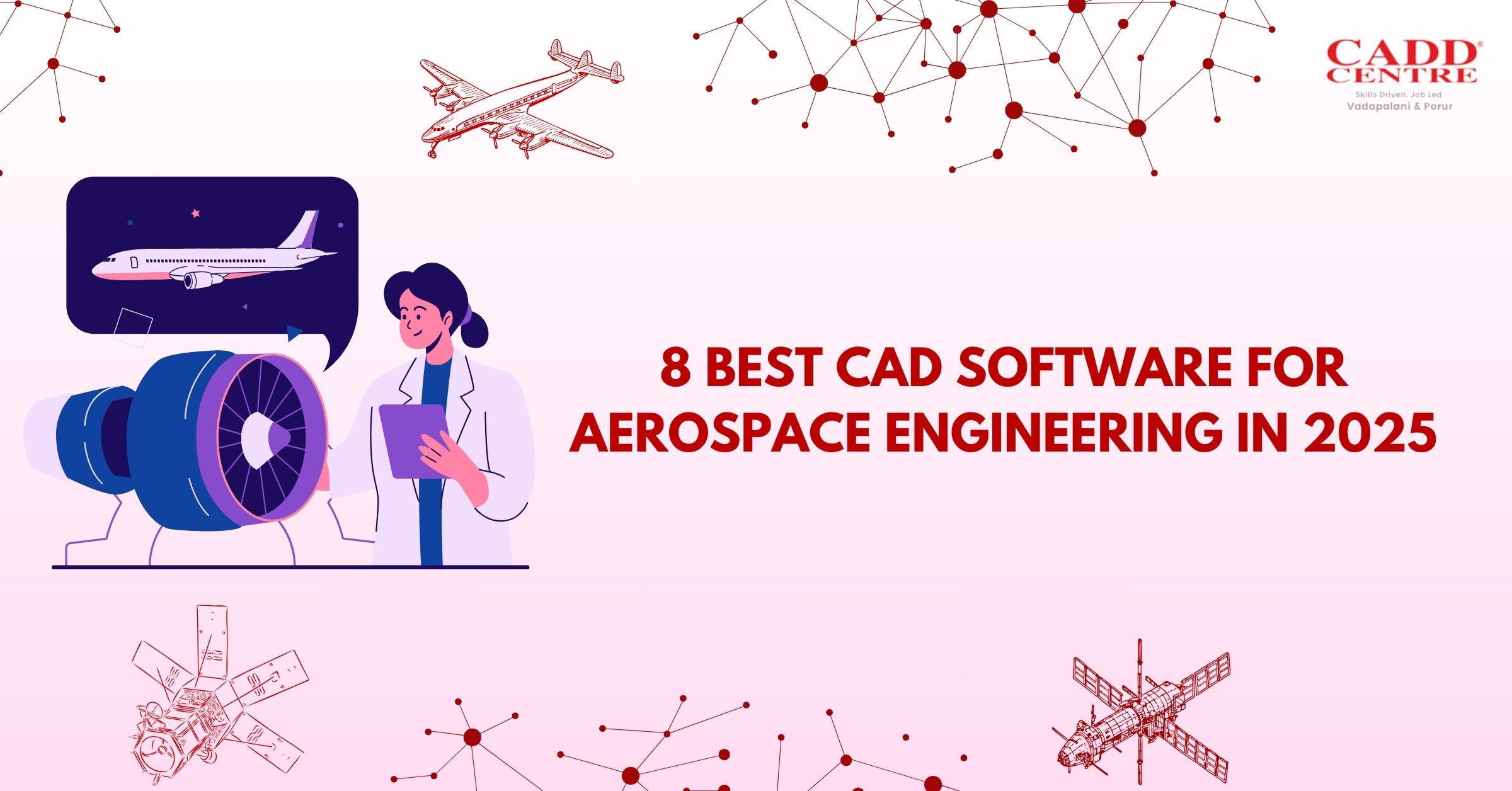
The ever evolving aerospace engineering domain demands precision, efficiency, and innovation at very high levels. As far as 2025, CAD software for aerospace engineering continues to be an anchor with regard to the aerospace design of sophisticated aircraft and spacecrafts. From conceptual sketches to Complicated 3D models, aerospace engineering CAD enables professionals to meet stringent industry standards while at the same time pushing technological boundaries.
The Blog content would include discussing the very best CAD software for aerospace from the perspective of its features, costs, and advantages. Whether you may be from the industry and looking for some tool such as Siemens NX, or you are a novice anticipating CATIA course in Chennai, use this blog to ramp up your aerospace design projects.
What is CAD?
What is CAD? Computer-Aided Design (CAD) is a modern electronic concept which provides engineers and designers with great efficiency in creating, modifying, and analyzing virtual models or digital representations for physical objects. Professionals now prepared with suitable CAD software develop their 2D drawings while threedimensions create virtual 3D models by exception. By 2025, CAD software for aerospace engineering will have become a must-have for aerospace engineering, especially extensive areas such as aerospace, in which complex geometries and rigorous testing are standard requirements.
What is CAD in Aerospace Design?
In aerospace CAD, the adoption of computer aided design tools enables aerospace engineers to create thorough airplane or spacecraft designs and their components in aerospace CAD. The structural analysis and design along with aerodynamic simulation and manufacturing processes get support from these modeling systems. CAD software in aerospace engineering works with simulation and production processes. This compatibility ensures designs are safe, perform well, and meet regulatory standards. This technology will serve as the foundation for future innovations in aerospace .
Why Is CAD Software Essential For Aerospace Design?
The aerospace industry needs top-notch precision and productivity; so, CAD software is essential. Programs like AutoCAD aerospace engineering solutions let engineers test real-world scenarios, fine-tune designs, and work together across the globe. By cutting down on mistakes and speeding up development, CAD software for aerospace engineering helps save time and money while sticking to aviation and space rules. In 2025, this CAD aerospace software drives progress in lightweight materials, aerodynamics, and bringing systems together.
8 Best CAD Software for Aerospace Engineering [2025]
Below, we dive into the 8 best CAD software for aerospace engineering in 2025, highlighting their capabilities and how they cater to the unique needs of the industry.
CATIA
Created by Dassault Systèmes CATIA (Computer-Aided Three-dimensional Interactive Application) leads the aerospace engineering field. Top companies like Boeing and Airbus use CATIA aerospace tools to handle complex projects in 2025. Its strong package helps with design, simulation, and manufacturing. Options like CATIA training in Chennai allow people to improve their skills. Its ability to scale up makes it a top pick for exact work and big assemblies.
Features
- Advanced 3D modeling and parametric design
- Built-in simulation for aerodynamics and structural analysis
- Team-friendly platform through the 3DEXPERIENCE system
- Support to design composite materials
Cost
- Subscription-based starting at about Rs 10,000 per year (changes based on license and modules).
Pros and Cons
- Pros: Strong tools for big projects, great teamwork features special aerospace modules for the industry.
- Cons: Expensive and hard for newcomers to learn.
SolidWorks
SolidWorks, a product of Dassault Systèmes, strikes a balance between power and ease of use in 2025. It’s a go-to choice for SolidWorks aerospace projects suited for small and mid-sized companies designing parts such as landing gear. Its user-friendly interface backed by SolidWorks training in Chennai, makes it easy for new engineers to pick up. It has grown beyond its mechanical design roots to meet aerospace industry needs head-on. If you want to learn a more about check our blog Top SolidWorks Training Centres in Chennai
Features
- Easy-to-use 3D modeling and assembly design
- Built-in tools to analyze stress and heat
- Tools for sheet metal design
- Smooth connection with CAM software
Cost
- Changes based on the type of license
Pros and Cons
- Pros: You can pick it up , it won’t break the bank for smaller jobs, and you’ll find plenty of help from other users.
- Cons: It struggles to handle huge aerospace systems as well as CATIA does.
CREO
PTC’s Creo software, formerly Pro/ENGINEER, is a parametric Creo CAD tool thriving in aerospace by 2025. Known as Creo Parametric, it handles small components to intricate assemblies like satellite designs. Its flexibility, bolstered by Creo training in Chennai, appeals to engineers needing simulation and adaptability in aerospace projects.
Features
- Parametric and direct modeling
- Finite Element Analysis (FEA) for structural testing
- Augmented reality design validation
- Additive manufacturing support
Cost
- CREO Design Essentials starting around ₹1,80,000
Pros and Cons
- Pros: Versatile modeling options, strong simulation tools, scalable for various project sizes.
- Cons: Interface can feel outdated, less dominant in aerospace compared to CATIA.
Autodesk Inventor
Autodesk Inventor Professional has become a popular 3D mechanical engineering design tool in aerospace by 2025. It offers simulation and automation features that appeal to mid-sized companies. Though not as specialized as other options, its connection to Autodesk’s ecosystem boosts its usefulness for CAD software for aerospace engineering processes.
Features
- Dynamic simulation
- stress analysis Parametric modeling with automation tools
- Connection to Autodesk’s cloud ecosystem
- Detailed documentation creation
Cost
- An annual Inventor subscription costs ₹1,49,860 and a monthly Inventor subscription costs ₹18,880.
Pros and ConsPros:
- Pros: Budget-friendly powerful simulation features smooth Autodesk integration.
- Cons: Less aerospace-specific compared to CATIA or Siemens NX.
Siemens NX
Siemens NX, a product of Siemens Digital Industries Software, stands out in complete workflows for aerospace giants such as GE Aviation in 2025. NX CAD training course options back it up, and it combines design, simulation, and manufacturing to handle complex systems like jet engines. Its approach across multiple disciplines matches CATIA in top-tier aerospace uses.
Features
- Advanced CFD and structural analysis
- Design integration across multiple disciplines
- Generative design to create lightweight parts
- PLM integration with Teamcenter
Cost
- Siemens NX prices in India can change based on things like customization and extra features needed.
Pros and Cons:
- Pros: Strong simulation great for complex systems tight manufacturing integration.
- Cons: Costly, needs a lot of training.
AutoCAD
AutoCAD, Autodesk’s flagship product, stands out for 2D drafting but also supports 3D modeling in 2025. AutoCAD for aeronautical engineering shines in technical drawings and schematics making it a key secondary tool in AutoCAD aerospace engineering settings to document and comply with regulations. For more information check our blog Best AutoCAD Training Institute in Chennai
Features
- Accurate 2D drafting and annotation
- Simple 3D modeling tools
- Teamwork in the cloud
- Large collection of design templates
Cost
- AutoCAD LT’s monthly plan costs ₹3,540.
Pros and Cons:
- Pros: Affordable, popular, great for 2D documentation.
- Cons: Basic 3D features limit complex aerospace designs.
ANSYS
ANSYS has a major influence on CAD software for aerospace engineering in 2025 mainly as a simulation tool. Its emphasis on fluid dynamics and structural analysis backed by ANSYS training center resources, makes it essential to validate safety. It works with tools like CATIA and NX to achieve aerospace precision.
Features
- Computational Fluid Dynamics (CFD) to analyze aerodynamics
- Finite Element Analysis (FEA) to test stress
- Thermal and electromagnetic simulation
- Integration with CATIA, SolidWorks, and NX
Cost
- ₹10,000 to ₹30 lakh or more for a single license
Pros and Cons:
- Pros: Unbeatable simulation accuracy crucial to validate safety.
- Cons: Not a standalone CAD tool expensive for full suite.
SharkCAD Pro
SharkCAD Pro, a product of Punch! Software stands out as a specialized CAD software for aerospace engineering in 2025. Its AeroPack plugin focuses on aircraft design providing tools to model airfoils and wings. This software offers a budget-friendly and easy-to-use option for smaller companies looking for targeted tools.
Features
- Mesh, solid, and surface modeling
- AeroPack tools to design airfoils
- wings Works with 3D printing
- Good option compared to high-end tools
Cost
- ₹ 203000 per year
Pros and Cons:
- Pros: Budget-friendly targeted aerospace tools simple to use.
- Cons: Not used in the industry with fewer advanced features.
These are the best CAD software for aerospace engineering. That you can look for.
Training and Skill Development for Aerospace CAD Software
To master CAD software for aerospace engineering, you need solid training. In 2025, you can find many options worldwide and nearby to boost your skills with these crucial tools. Here are key training opportunities for the top software solutions:
- CATIA: CATIA course in Chennai give you hands-on experience with this industry-leading software helping you learn its advanced design and simulation features.
- SolidWorks: Including the best SolidWorks training in Chennai, SolidWorks courses in Chennai offer full programs for new engineers who want to get good at this easy-to-use yet powerful tool.
- Creo: Aims to improve your skills in parametric design giving you the know-how to use Creo software well in aerospace projects.
- Siemens NX: Siemens NX course, and Siemens Unigraphics NX training teach you advanced skills for Siemens NX getting you ready for its multi-disciplinary design and manufacturing integration.
- ANSYS: ANSYS training center in Chennai, and ANSYS training center for aerospace give you key simulation skills focusing on fluid dynamics and structural analysis that are crucial for aerospace safety and performance.
These training options make sure engineers can use CAD software for aerospace engineering to its full potential supporting both personal growth and new ideas in the industry in 2025. If you want to learn more about CAD Software or you want to learn specific software you can check CADD Center Porur and Vadapalani, one of the best training institutes in chennai.
Benefits of Cad Software Essential For Modern Aerospace Design
CAD software has a revolutionary impact on aerospace design in 2025. CAD software for aerospace engineering provides clear advantages that boost every phase of the development process, from idea creation to manufacturing. Let’s dive into these benefits:
Enhanced Precision And Accuracy
- CAD software for aerospace engineering makes sure models are super accurate, which is key for parts like turbine blades and fuselage panels. Tools such as CATIA and Creo Parametric use parametric design and smart algorithms to get rid of human mistakes hitting tolerances down to micrometers.
- This level of accuracy is crucial to meet aerospace safety rules and to get the best performance in tough conditions, like flying at high altitudes or exploring space.
Improved Simulation
- The simulation tools embedded in the software ensure engineers properly assess designs against real-world conditions. Programs like ANSYS and Siemens NX offer Computational Fluid Dynamics (CFD) and Finite Element Analysis (FEA) to simulate aerodynamic forces, heat loads, and structural stresses. In aerospace, where failure is not acceptable, this becomes a significant advantage: reducing the need for physical prototypes to demonstrate strength before manufacturing.
Efficiency And Speed
- Automation and parametric modeling in aerospace CAD have a significant impact on speeding up design iterations. Take SolidWorks aerospace solutions as an example – they allow quick changes to assemblies. Autodesk Inventor Professional, on the other hand, makes repetitive jobs like bolt patterning automatic
- . This boost in speed cuts down development times giving aerospace companies the chance to launch new ideas – such as cutting-edge drones or reusable rockets – much quicker than before as we look ahead to 2025.
Cost Reduction
- CAD software spots problems through simulation cutting down on the need for pricey physical models and fixes. AutoCAD for aeronautical engineering creates exact drawings that make manufacturing smoother, while SharkCAD Pro makes the most of materials with its 3D printing features.
- These improvements lead to big savings, which is key in a field where development costs run high.
Ease Of Collaboration .
- Such a streamlined fact can be made possible using cloud platforms in CAD software for aerospace engineering. Teamwork can easily become seamless across entire, as could be the case for products from CATIA’s 3DEXPERIENCE and Siemens NX’s Teamcenter. Engineers from different continents can work together in real-time, sharing models, simulations, and other concepts.
- This connectivity speeds up decision-making and keeps everyone on the same page, which is crucial for big aerospace projects such as satellite groups or passenger planes.
Enhanced Documentation And Compliance
- CAD software creates detailed drawings, Bills of Materials (BOMs), and compliance reports with ease. AutoCAD aerospace engineering tools are great at making annotated 2D schematics needed for regulatory submissions, while Siemens NX works with Product Lifecycle Management (PLM) systems to keep track of design changes.
- This makes sure companies follow standards like FAA or EASA rules, which is a must in aerospace engineering.
Historical Data Retention
- Digital models created by the best CAD software for aerospace keep design data to refer to in the future, maintain, or upgrade. For example, CATIA aerospace projects store complex assemblies allowing engineers to look at and improve designs years later.
- This storage helps long-term projects—such as spacecraft that last for decades—and makes it easier to follow rules about keeping historical records.
In 2025, CAD software for aerospace engineering sparks new ideas, from CATIA to SolidWorks aerospace answers. These top CAD software tools coupled with lessons like Siemens Unigraphics NX training, help engineers to build effective secure aerospace systems. Pick to push your projects ahead.
FAQ
Which CAD software is most commonly used in the aerospace industry?
CATIA, a very well-known software solution in the aviation sector. The larger companies in aerospace such as Boeing and Lockheed Martin are using it. Advanced 3D modelling and simulation capabilities make this the number-one choice for complex projects involving aircraft bodies and spacecraft systems. By 2025 that software should truly be specified for precision and reliability.
What features should aerospace engineers look for in CAD software?
For detailed modeling, aerospace engineers require strong 3D modeling capabilities, built-in simulation such as CFD and FEA for performance testing, and PLM integration for a nicely smooth workflow. The software should also be compliant with aerospace CAD standards and have collaborative functionalities. All these requirements are an absolute must to cater to today’s engineering challenges.
What is the best CAD software for aircraft component design?
CATIA and Siemens NX are two shining stars in aircraft parts design. Parametric modeling, advanced simulation to analyze stress and air flow, and special tools that deal with complex shapes such as wings and engines are offered by both applications. By 2025, they ensure compliance of designs with strict aerospace regulations.
How does CAD software improve efficiency in aerospace design?
Efficiency is increased with CAD software through automation of repetitive tasks such as creating parametric changes and providing powerful simulations that lessen the need for prototyping. Solutions such as SolidWorks aerospace speed up iterations, saving time and cost while ensuring correctness in designs throughout the entire process.
What factors should I consider when choosing aerospace CAD software?
Along with cost as an important factor, a good CAD software for aerospace engineering is selected considering the capabilities handling complexity and user-friendliness. It would be worthwhile to check for training options, like quality SolidWorks training in Chennai. Other types of considerations should include the strength of the simulation tools, its actual use in the industry, and the integration with your system for maximum benefit.
Tags: Aerospace CAD, aerospace engineering, AutoCAD Aerospace Engineering, AutoCAD for aeronautical engineering, CAD Software for Aerospace Engineering, SolidWorks Aerospace